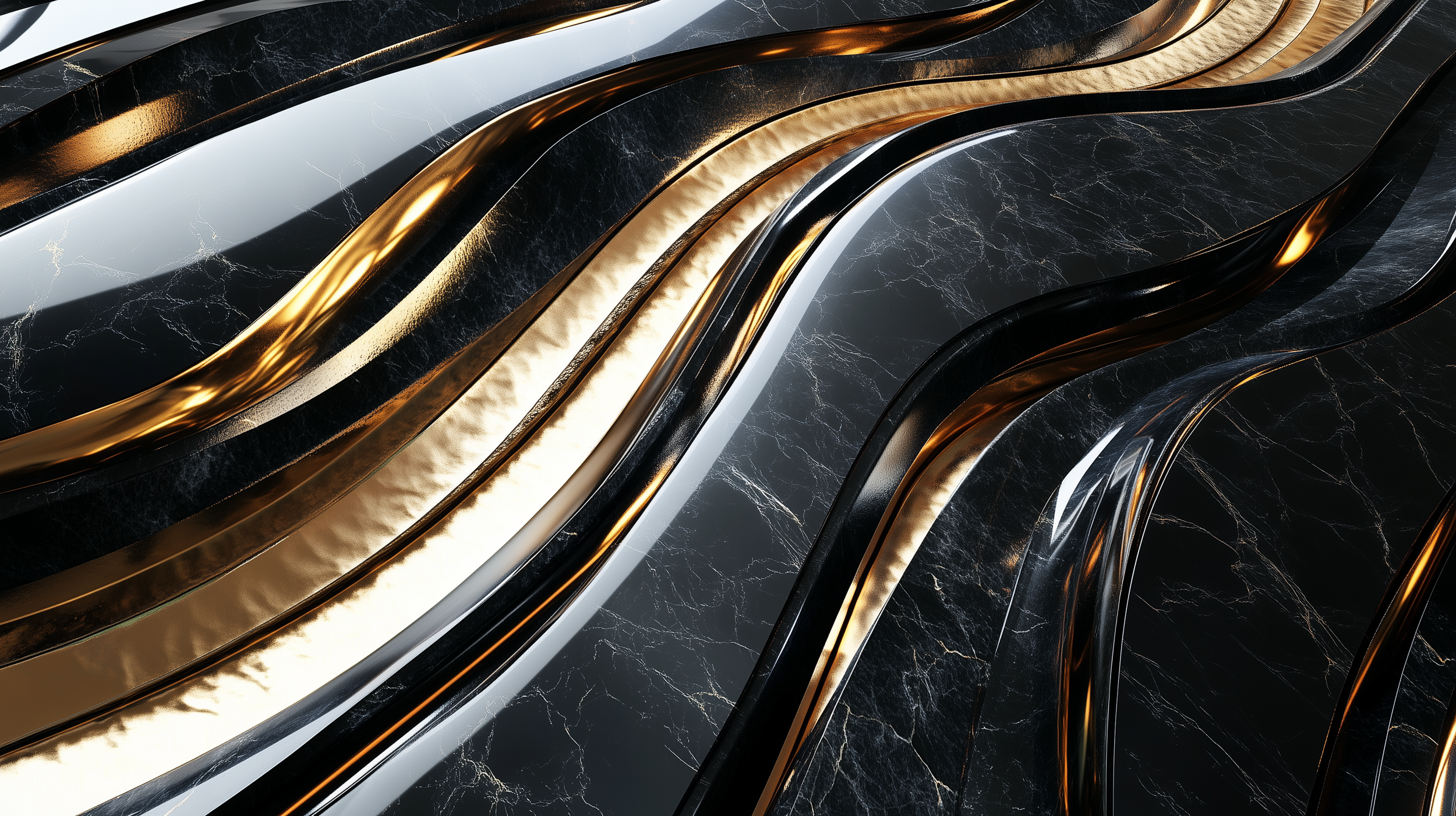
Market Potential & Impact
Project Aether
Market Capture for the Modular Pressure Vessel (MPV)
Focus: Manufacturing Industry - Curing Polymers and Concrete
Relevant Market Size & Growth
Pressure Vessel Market (Broad): $51.9B (2024) → $68.2B (2030), CAGR 4.7%.
Pressure Vessel Composites Market: $4.77B (2023) → $7.5B (2032), CAGR 5.16%. Relevant to polymer curing.
Precast Concrete Market: $103B (2023) → $159B (2030), CAGR 5.5%. Niche for pressure-cured concrete.
Polymer Concrete Market: $2.1B (2023) → $3.4B (2030), CAGR 7.1%. Ties to polymer curing.
Estimated Target Market: $5-10B annually by 2030 for curing-specific applications
Value Proposition
Cost Reduction: $5K-$20K vs. $50K-$500K for industrial systems.
Scalability: Modular design for small-batch polymer and concrete curing.
Accessibility: Targets SMEs, DIY fabricators, and startups
Efficiency: Faster curing, improved material properties (e.g., void-free polymers, stronger concrete).
Market Capture Potential
Competitive Landscape: Dominated by Pentair, Steelhead Composites, etc. Underserved niche: SMEs, prototyping labs, hobbyists.
Penetration Scenarios:
Low-End (1-3%): $50-100M/year, 5K-10K units at $10K each.
Mid-Range (5-10%): $250-500M/year, 25K-50K units.
High-End (15-20%): $750M-$1B/year, displacing industrial systems.
Growth Drivers: Demand for composites, sustainable construction, additive manufacturing.
Factors Influencing Capture
Patent Strength: Broad patent enhances exclusivity.
Manufacturing Costs: $2K-$5K/unit enables competitive pricing.
Regulatory Hurdles: ASME compliance may slow consumer adoption.
Adoption Rate: Early adopters (e.g., 3D printing, precast startups) drive initial growth.
Realistic Estimate
Short-Term (1-3 Years): $10-50M/year, early adopters.
Mid-Term (5-7 Years): $100-300M/year, SME penetration.
Long-Term (10+ Years): $500M-$1B/year, broader adoption.
Likely Range by 2030: $250-500M/year, up to $1B with partnerships/licensing.
Conclusion
The patent holder could capture $250M-$1B annually by 2030, targeting SMEs and rapid prototyping markets. Licensing to established players could maximize scale.
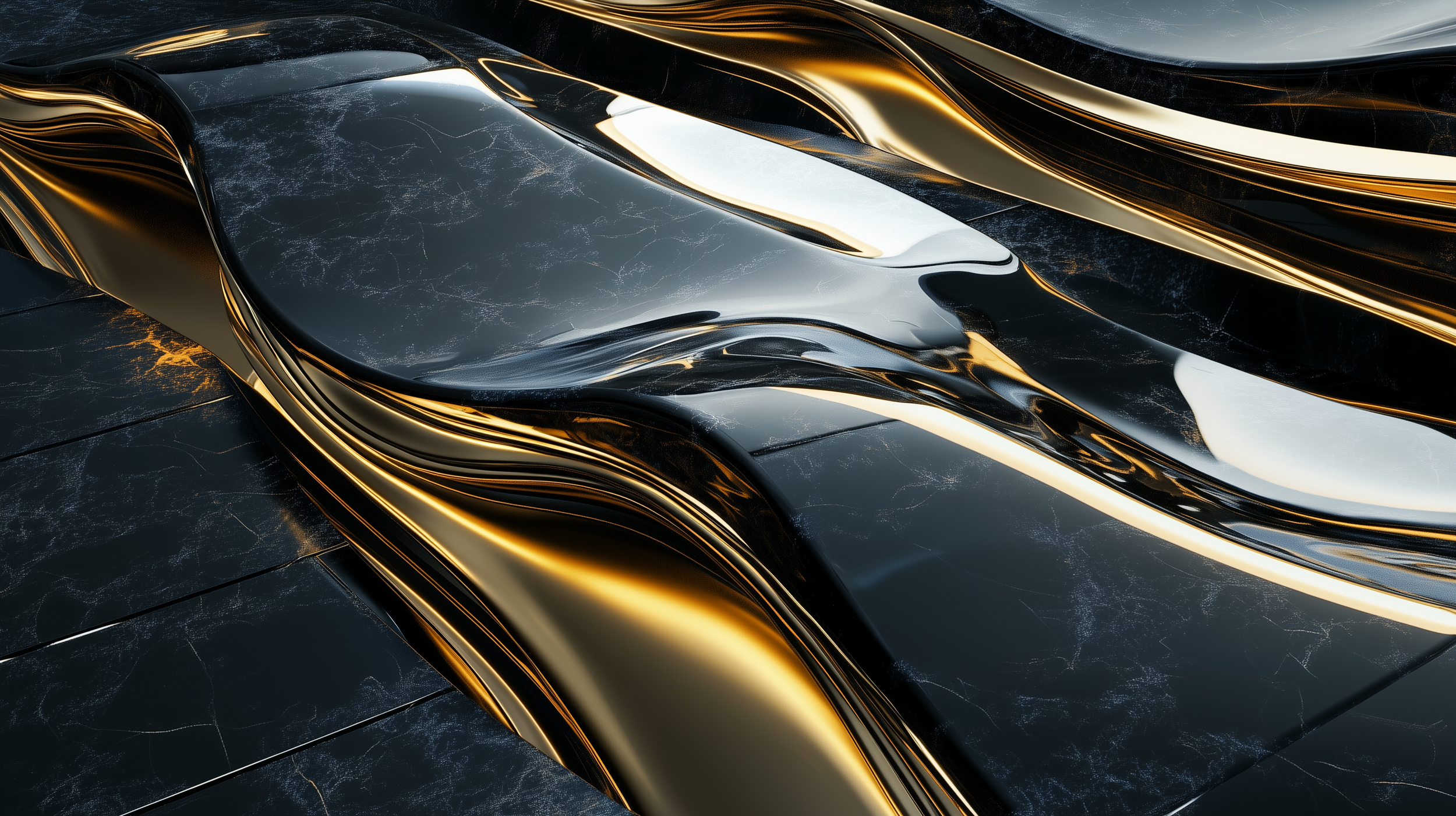
Revolutionizing Manufacturing: MPV Technology
Unlocking a $1 Billion Opportunity
The Innovation
A patented, consumer-friendly modular pressure vessel that transforms curing for polymers and concrete:
Affordable: $5K-$20K vs. $50K-$500K industrial systems.
Scalable: Interchangeable design for small-batch production.
Efficient: Faster curing, stronger materials—void-free polymers, durable concrete.
The Market
Target: $5-10B curing segment by 2030 (composites, precast concrete).
Growth: 5-7% CAGR in polymers and concrete markets.
Niche: SMEs, prototyping labs, and DIY fabricators—underserved by industrial giants.
The Opportunity
Capture Potential: $250M-$1B annual revenue by 2030.
Year 1-3: $10-50M from early adopters.
Year 5-7: $100-300M with SME penetration.
Year 10+: $500M-$1B via licensing and scale.
Edge: Disrupts costly autoclaves, taps into additive manufacturing and sustainable construction trends.
Why Invest?
Patent Power: Broad protection secures market exclusivity.
Low Cost, High Margin: $2K-$5K production cost, $10K+ sale price.
Scalable Model: Direct sales + licensing to industry leaders (e.g., Pentair).
Impact: Empowers small manufacturers, accelerates innovation.
The Vision
From 3D-printed composites to precast concrete, our technology democratizes advanced manufacturing. Be part of a $1B future—invest today!
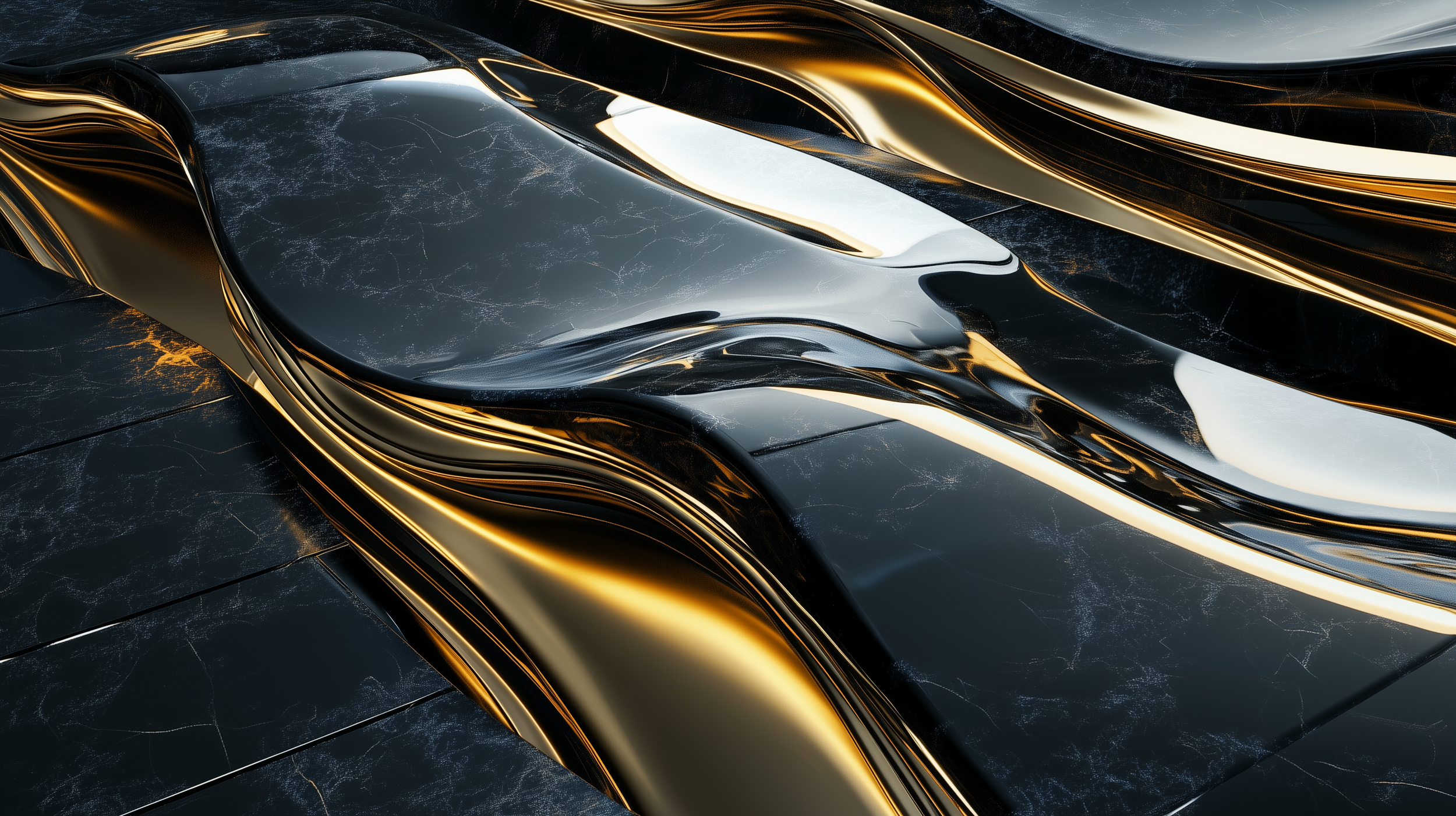
Polymer Curing Applications for a MPV
A consumer-friendly, commercially available modular pressure vessel can revolutionize polymer curing in manufacturing by offering an affordable, scalable solution. Below are key applications, emphasizing their relevance to small-scale producers, prototyping labs, and DIY fabricators.
Resin-Based Composites
Use: Curing epoxy, polyester, or polyurethane resins for lightweight, high-strength parts.
Examples:
3D Printing: Post-curing resin prints (e.g., figurines, prototypes) to remove bubbles and enhance durability.
Fiberglass: Producing boat hulls, car panels, or drone frames.
Carbon Fiber: Small-batch aerospace or sports equipment components.
Benefit: Pressure eliminates voids, improving clarity and strength (e.g., up to 20-30% stronger tensile properties vs. ambient curing).
Adhesives and Sealants
Use: Curing industrial-grade epoxies or silicone sealants under pressure.
Examples:
Electronics: Bonding circuit boards or encapsulating components.
DIY Repairs: Fixing furniture or automotive parts.
Benefit: Faster cure times (e.g., hours vs. days) and uniform bonding, critical for reliability in small-scale production.
Foam Production
Use: Expanding and curing polyurethane or polystyrene foams.
Examples:
Packaging: Custom foam inserts for shipping.
Insulation: Lightweight panels for home or RV use.
Art/Props: Sculptures or theatrical set pieces.
Benefit: Controlled pressure ensures consistent cell structure, reducing waste and improving foam quality.
Coatings and Surface Treatments
Use: Applying and curing polymer coatings (e.g., epoxy paints, protective films).
Examples:
Metal Finishing: Corrosion-resistant layers on tools or machinery.
Woodworking: Durable finishes for furniture or flooring.
Automotive: Clear coats for custom parts.
Benefit: Pressure minimizes defects (e.g., orange peel), delivering professional-grade finishes at a lower cost.
Experimental Polymer Development
Use: Testing new polymer formulations under controlled pressure.
Examples:
R&D Labs: Developing biopolymers or high-performance resins.
Startups: Prototyping flexible electronics or medical devices.
Hobbyists: Crafting unique materials for art or engineering.
Benefit: Modularity allows rapid adjustments (e.g., pressure levels, vessel size), accelerating innovation.
Why It Matters
Market Fit: Aligns with growing demand for composites ($4.77B market in 2023 → $7.5B by 2032, CAGR 5.16%) and additive manufacturing.
Advantage: Replaces costly vacuum chambers or autoclaves with a $5K-$20K modular solution, opening polymer curing to SMEs and DIYers.
Impact: Faster production (e.g., 2-3x speed), higher quality, and accessibility drive adoption in prototyping, custom manufacturing, and niche markets.